SUSTAINABILITY SPOTLIGHT | 14 After 12 months, teams reported a 15%–30% reduction “This wasn’t about us coming in and telling them what in thermal and electric energy consumption at both they need to do, then leaving. EPK had already been sites. There was also a signi昀椀cant increase in tea engaging in various energy-saving activities. This was produced per unit of fuel wood (kWh/m3). about walking alongside them, listening to them, and getting them involved. “Now, there is the controlled start-up of machines after a power outage,” says Chris Ballard, Technical Director “For example, we encouraged the leadership team to of EPK. “No machines are left idle or running when not establish their targets, to establish local improvement in use. There is also proper work output by employees teams to undertake surveys and implement their action who now understand that their work has a direct impact plans and provide recognition for all the hard work on energy savings. The shop-昀氀oor teams appreciate the involved.” load-shedding regime and no longer see it as a limiting factor in withering operations. For Fred Oberi, a drier operator at Kepchomo Factory, the changes have resulted in professional growth: “I was “We have also adopted a new way of covering 昀椀rewood motivated to get involved since I was made to realise in the yard, resulting in high 昀椀rewood utilisation that my role as a drier operator was critical in sustaining e昀케ciency compared to previous years. Data on the company’s business as opposed to how I have electrical energy use is collected from each section of been perceiving it. In addition, the awareness of energy the factory. The data is compared between all factories, saving has improved my ability to avoid wastage of highlighting ine昀케cient sections of a factory that must important resources at work and on a personal level.” be improved. Chris Ballard echoes the crucial role that the IfM “These actions have led to signi昀椀cant energy savings at played in engaging the sta昀昀: “Everything was in place both sites, and there has been an overall improvement mechanically, but the next step was to get the people in factory performance across all areas,” says Chris. involved. Crucial to this was engaging the shop-昀氀oor workers in the energy-saving plan. This worked because How many cows have we saved? they are the ones who understand the operations Gary explains that one of the key success stories has of every machine, since they are the users, and they been getting the local team engaged in the changes understand the challenges and areas for improvement. and making the sustainability gains relevant to their They are the ones who know possible areas for context. “We engaged the factory workers on their improvement, and therefore they had to own the terms and in their language. We did this by converting process 昀椀rst. energy into something recognisable: not gigajoules, but “The shop-昀氀oor teams took the project as their own and ‘How many cows can you buy with the savings?’ This not a ‘Cambridge University’ project. Engaging the sta昀昀 gave us all a laugh but e昀昀ectively equated to how much created ownership of the process and how the process energy had been saved. It brought understanding to the directly impacted their personal lives,” says Chris. room – that energy wasn’t something intangible. By the end of the project, they worked out that they had saved “We’ve been working on factory e昀케ciency for many 2,000 cows – the size of the president’s herd!” years,” Chris continues. “So, it’s not just something Gary recognises that local e昀昀orts have been mirrored that’s happened. The IfM clari昀椀ed precisely what we by a strong commitment from EPK HQ to try something should be doing, focusing on, and getting the factory new, as well as supportive managerial and technical personnel involved. leadership on the ground in Kenya: “The open and “We knew where all the problems were, but it’s getting positive culture of the Kenyan factory management intentions turned into action, which is challenging, and and factory sta昀昀, coupled with our empathy and that is where the IfM helped.” understanding of ‘real’ factory challenges and simple methodology, meant we could see impactful changes almost immediately.
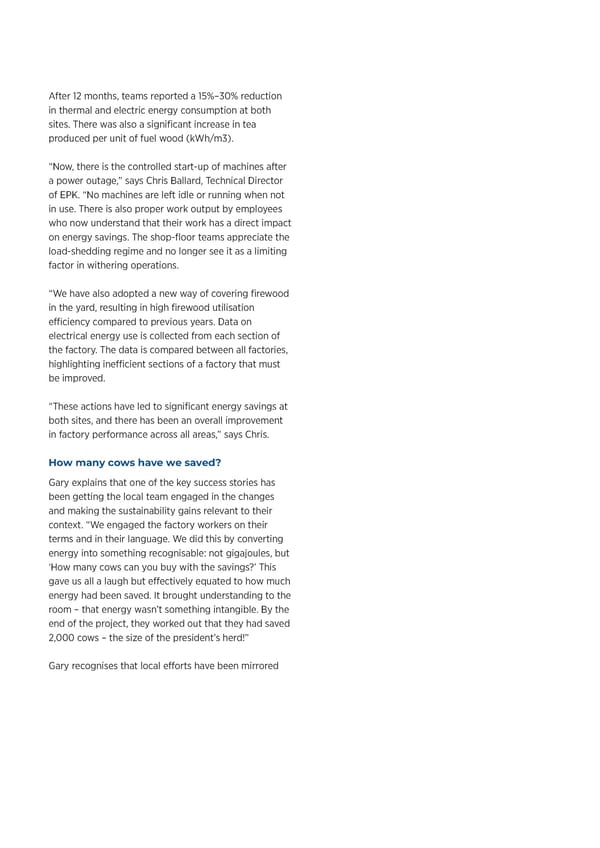